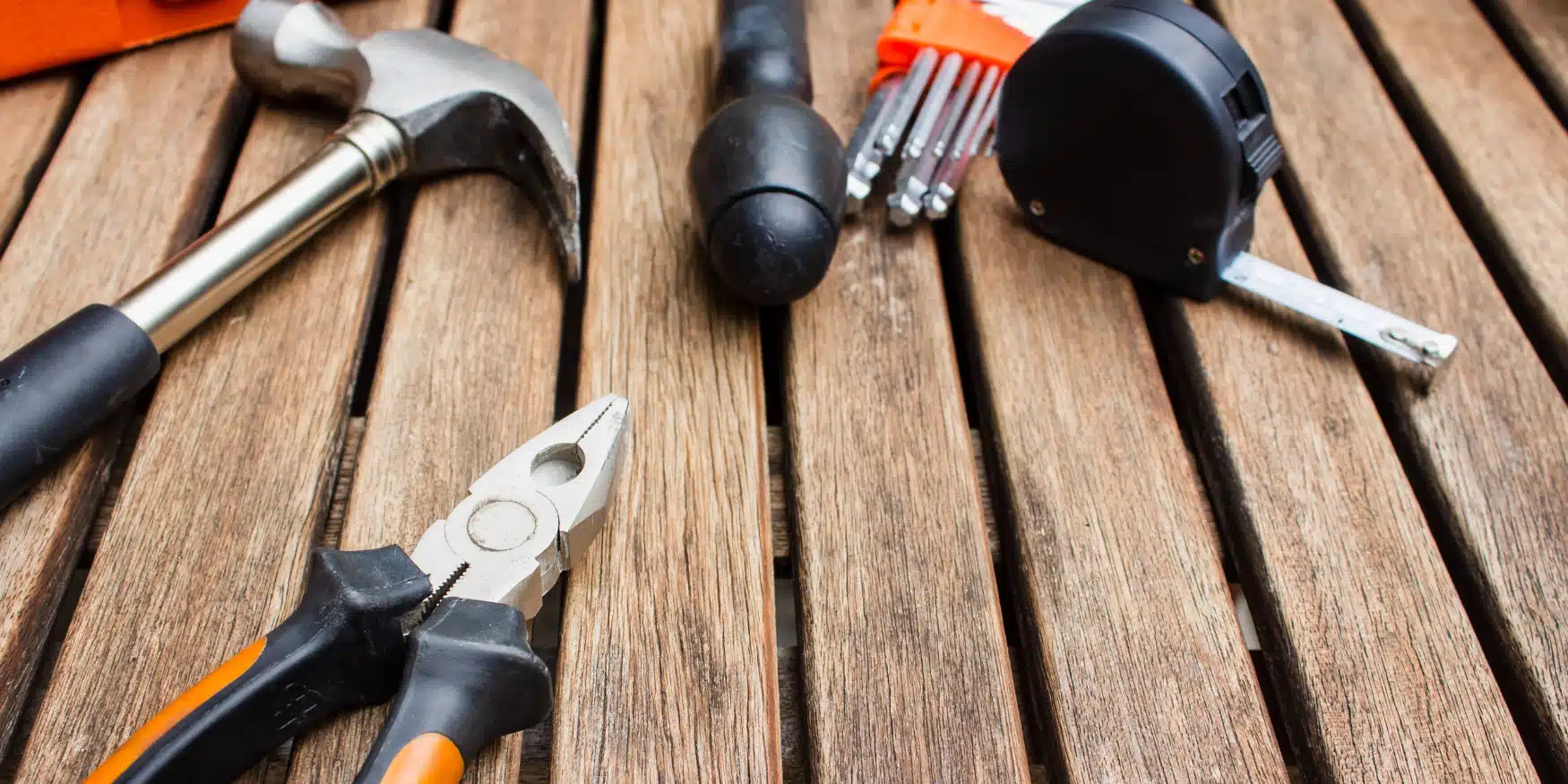
Successful construction projects are the result of effective material management. Planning and controlling all materials and equipment for a construction project helps to keep production running smoothly. Construction materials typically account for up to 60% of the cost of a capital project; highlighting the need for effective material management. With streamlined construction material management, you can minimise waste, source higher quality materials, improve your overall budget and increase overall safety and productivity.
The construction industry is one of the most capital-intensive industries in Australia, generating over $360 billion in revenue and having a share of 9% of the total GDP in the country. Despite this, many construction companies fail to handle their vast inventory of equipment and materials effectively.
Here, we discuss some of the challenges of material management and the key strategies you can use to improve construction project efficiency.
One of the biggest challenges construction companies face is the effective management of materials. From planning, purchasing and tracking to obtaining accurate bills and setting up sufficient storage space; all these aspects need to be correctly categorised to avoid possible problems such as going over deadlines or budgets.
To avoid these challenges, you need to implement some basic strategies that will improve your construction site efficiency and keep projects on task.
One of the best ways to streamline material management is with project management software. Fergus can help to improve your current workflow by simplifying the project planning process, making it easier to plan and prioritise all required tasks, resources, timelines and constraints.
In the construction industry, proper planning can reduce cost and waste and ensure a profitable project. Let’s explore some of the best practices of proper material management, below.
On a construction site, a storage space provides protection for materials that are kept during the construction process. Without sufficient storage, you run the risk of damage due to weather or even theft.
One of the things you’ve likely run into is the lack of sufficient storage space. In this scenario, it’s common to store materials in different places, even off-site. The trouble that comes with that is that it makes it difficult to track materials which can then lead to material shortages or inaccurate inventory counts. The solution? Proper and careful planning of delivery times and quantities along with practical storage solutions. Some things that can help:
Reduce the risk of an accident by correctly storing hazardous materials in a safe zone away from the construction site.
Material kitting can help to streamline material management in construction. Kitting is the process of compiling different materials and equipment into kits/groups based on their SKU or equipment type to free up inventory space and reduce the time it takes to hunt for materials for assembly – making production more efficient.
You should think about material kitting if you find that too much time is wasted when locating materials in the warehouse or storage floor. This can easily happen in situations where you’re dealing with a large variety of small components or customised components varying in size, colour and shape. You can handle material kitting by:
Another common challenge in the construction industry is maintaining accurate inventory counts and costs. Having an effective inventory management process is necessary for making sure you have the right materials and quantities at the right time. It’ll also help you meet your tax obligations and reduce any inaccuracies that may lead to material wastage. In fact, between 24-36% of those within the construction industry are still using paper-based means to track and manage data for tasks including inventory management.
Managing labour materials and costs comes down to the effective usage of tracking systems. For instance, an equipment tracking system like Just in Time Stock Control allows you to buy materials only when you need them. In conjunction with a software management system, you can ensure that the materials you order are delivered on time and in the right quantity, reducing the risk of overbuying and helping you to avoid losses on materials.
Download our free Profit & Loss calculator to find out how much you’ve spent on materials.Download Free
Material handling in the construction world refers to the delivery, movement, storage and control of materials. From inspection to storage right through to assembly and use, the material handling process should be easy and streamlined to ensure everyone on site can get on with their job safely and efficiently.
Aside from ensuring adequate worker safety protocols, one of the biggest challenges you may face in the handling of materials is what to do with unwanted or unused construction materials.
One simple solution to managing unused materials is to return all unused stock to the supplier for credit. This system allows you to get rid of any unwanted or unused stock without the cost or logistics involved in driving it back to the supplier.
Other ways to ensure effective material management when handling materials include:
Quality assurance of construction materials is the responsibility of the purchase department to ensure all materials are of high quality, safe to use and have met industry testing and control methods/standards. Without implementing quality control & assurance in your material management process, you risk impacts from poor quality materials including loss of time, money and reputation, not to mention the potential for someone to get hurt or worse.
You can achieve the required quality & assurance for incoming construction materials by:
Planning what construction materials and quantities will be needed for a specific job can be a difficult and oftentimes overwhelming task. Therefore, having a project planning strategy in place is a wise way to make your job easier.
Poor material planning can result in significant delays in the project, it can lead to key materials becoming unavailable, and result in poor productivity levels on the construction site. All of which can become extremely costly to you and your business.
If you’re struggling to keep an accurate bill of materials then it’s a good time to invest in Fergus’s job management software which can help you keep track and calculate the materials needed to complete a project whilst ensuring that the right inventory is available exactly when you need it.
Maintaining an effective material management system is absolutely crucial to the success of a project. In the construction industry, it is vital that you consistently monitor and audit inventory and the handling of materials to guarantee good material management. Utilising management software can help make this task easier. The best thing you can do as a construction worker is to plan ahead. This will reduce any risks surrounding common challenges and ensure all your materials are used with optimal efficiency. By improving your construction material management, you can reduce the cost of materials, handle materials more safely, ensure adequate storage of materials on site, reduce waste and increase the productivity of a project so that it can be completed on time.
If you’re looking for a more effective way to manage your construction projects and materials, Fergus can help. We offer digital solutions to improve your material management process, giving you an organised and cost-effective business solution. Start your free trial with Fergus here.
Stop drowning in admin & paperwork. Start focusing on the jobs that make you money.
Our 20,000+ trades businesses have slashed their admin, are getting paid faster, and are finally enjoying their weekends again.